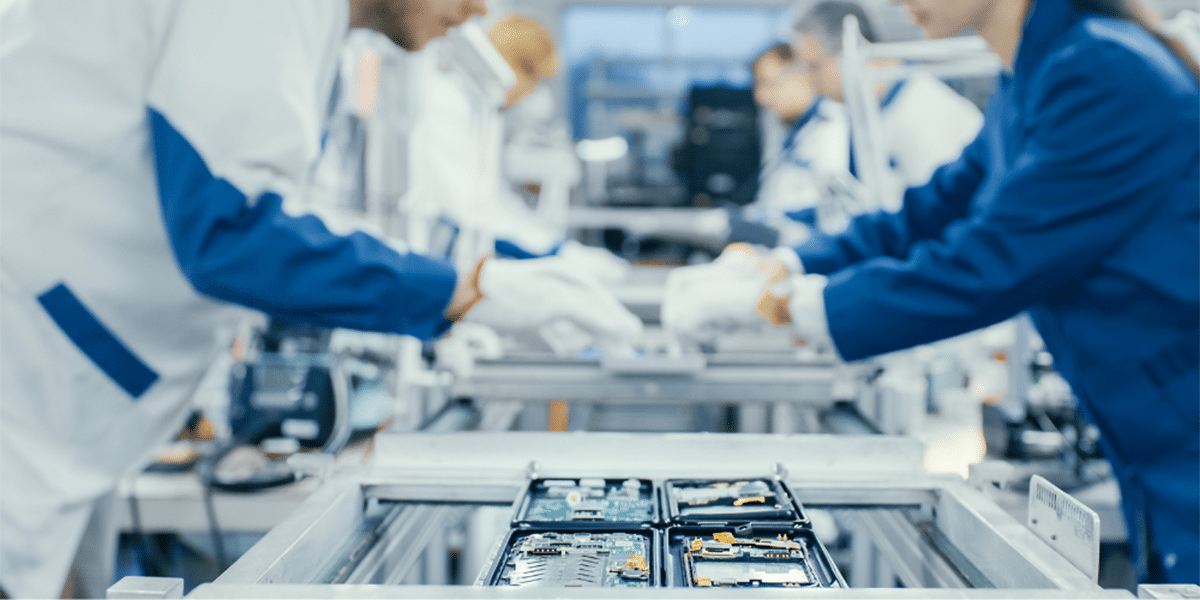
Assembly Line Factory Workers Training Tips to Strengthen Your Team
September 19, 2022 | Staffing Blog
With the introduction of new technology, robotics, and equipment to execute tasks in a manufacturing environment, the role of assembly line factory workers has changed. Employees that work on the assembly line must be able to perform higher caliber duties than their predecessors decades ago.
That’s why it’s important to provide training to workers who support the assembly line so that they can execute critical tasks. Offering training will strengthen your team, increase productivity, and ensure quality output in the factory.
Training to Offer Assembly Line Factory Workers
Consider how your company can provide targeted training to your employees to increase their capabilities.
1. Provide Equipment Training
There are many different pieces of equipment used on the assembly line. And, with the introduction of advanced new equipment such as automated robots, your employees may not understand the ins and outs of each piece of equipment. For example, they may only know how to utilize the equipment, but they don’t know how it actually works.
Take the time to gather input from your workers to understand their comfort level with each piece of equipment used on the assembly line. Ask questions so that you can identify ways to provide training that will create a deeper level of understanding:
- Do they understand the terminology for each piece of equipment?
- Can they explain to someone else how the equipment works?
- Do they know how to fix equipment when it’s broken?
2. Offer Cross-Training
Not every employee will be available to work their shift at all times. Employees will call out sick, take vacation time, be called away for other duties, or have other reasons why they cannot work their shift. You don’t want to be stuck in a situation where only a handful of employees know how to perform specific duties.
It’s important to provide each employee with cross-training so that they can fill gaps or provide relief to certain workers. This way, the assembly line won’t skip a beat, and productivity will continue to flourish.
We recommend taking the time to identify opportunities for employees to receive additional training on critical tasks. This will help them grow their knowledge of different aspects of the assembly line so that they can quickly fill a spot when needed.
3. Focus on Safety Training
As you know, safety is critical in a factory setting. The reality, though, is that not everyone may feel 100 percent confident in how to utilize certain pieces of machinery or equipment.
We encourage you to regularly ask employees if they have concerns, see issues using certain pieces of equipment, or need additional support performing their duties. Then, you can use their responses to implement specific safety programs to increase understanding and confidence working on the assembly line.
4. Implement QA/QC Training
It’s not enough for products to move down the assembly line to be ready for packaging and shipping. Finished products need to be inspected for quality before leaving the facility. This is where the human element is critical to review the integrity of each finished product.
A great way to strengthen your team is to provide workers with Quality Assurance/Quality Control (QA/QC) training. Your team will be better equipped to identify issues, stop the assembly line if needed, and take corrective actions. Consider providing training that satisfies these questions:
- Do employees understand each critical step in the QA/QC process?
- Can they quickly identify a flaw in a product?
- Do employees know who to contact if they see a problem area?
- Are employees looped into the resolution process to see how a problem was resolved?
5. Consider Management Training
Some employees are ideal candidates to transition from an assembly line factory worker to manager. Once you identify these high-performing and high-potential employees, consider providing them with management training. You can help these individuals understand how the entire factory functions instead of just their part on the assembly line.
There is another opportunity to provide training on managerial soft skills. This type of training will help future managers understand how to communicate at all levels in the company, manage workers, relate to their direct reports, and become a company leader.
Ready to Strengthen Your Team in the Factory?
Our encouragement to employers is to focus on ways that you can optimize human performance in the factory. Training is a great way to support assembly line factory workers so that they can help your company achieve productivity and performance goals.
Need support elevating the quality of human performance in your factory? Talk to the experts at Allegiance Staffing. We can help you identify a labor solution that fits your company’s needs.
Get in touch with us today to discuss practical ways to implement training that will strengthen the capabilities of your team. We look forward to supporting your company.